What is Porosity in Welding: Typical Resources and Effective Solutions
What is Porosity in Welding: Typical Resources and Effective Solutions
Blog Article
Comprehending Porosity in Welding: Exploring Causes, Impacts, and Prevention Methods
As experts in the welding industry are well conscious, understanding the causes, results, and prevention methods connected to porosity is important for attaining robust and trustworthy welds. By delving into the origin creates of porosity, examining its damaging results on weld quality, and checking out reliable avoidance techniques, welders can improve their expertise and abilities to produce top notch welds consistently.
Usual Reasons For Porosity
Contamination, in the kind of dirt, oil, or rust on the welding surface area, creates gas pockets when warmed, leading to porosity in the weld. Improper protecting occurs when the protecting gas, commonly utilized in processes like MIG and TIG welding, is not able to totally safeguard the liquified weld pool from reacting with the bordering air, resulting in gas entrapment and succeeding porosity. Furthermore, poor gas coverage, typically due to wrong flow rates or nozzle positioning, can leave components of the weld unprotected, enabling porosity to develop.
Results on Weld Quality
The visibility of porosity in a weld can dramatically endanger the total top quality and stability of the welded joint. Porosity within a weld produces voids or cavities that weaken the framework, making it a lot more prone to splitting, rust, and mechanical failure.
Furthermore, porosity can prevent the efficiency of non-destructive testing (NDT) techniques, making it testing to find other defects or suspensions within the weld. This can lead to substantial security concerns, specifically in important applications where the structural stability of the bonded elements is paramount.
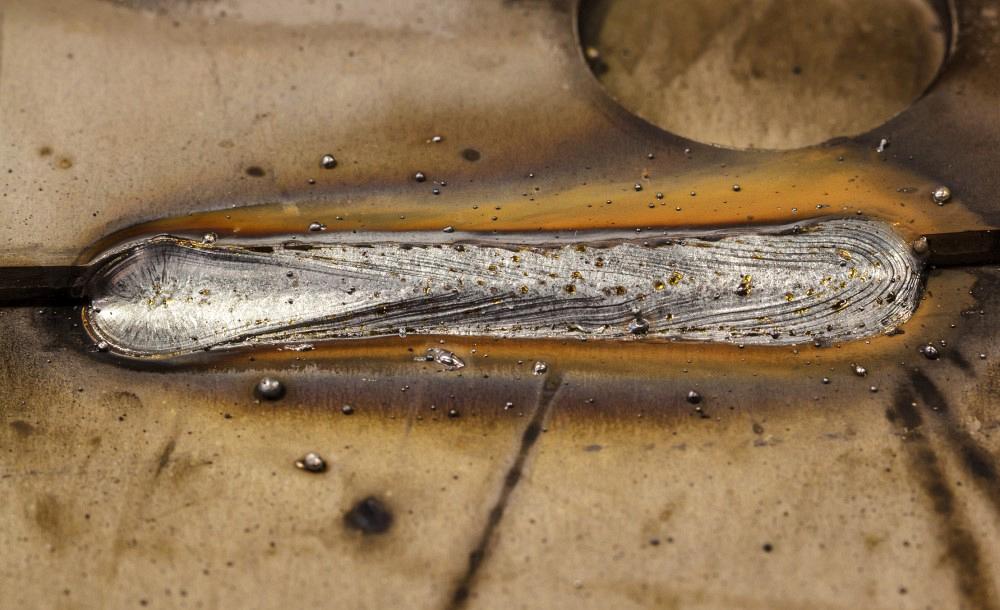
Prevention Techniques Review
Provided the destructive effect of porosity on weld quality, efficient avoidance techniques are essential to keeping the structural stability of bonded joints. One of the key prevention methods is thorough cleaning of the base products prior to welding. Contaminants such as oil, grease, corrosion, and moisture can add to porosity, so making sure a tidy work surface area is important. Appropriate storage of welding consumables in dry problems is also vital to protect against wetness absorption, which can result in gas entrapment during welding. In addition, selecting the ideal welding specifications, such as voltage, current, and travel rate, can assist lessen the threat of porosity development. Making certain sufficient protecting gas flow and protection is one more essential prevention strategy, as insufficient gas coverage can lead to atmospheric contamination and porosity. Proper welder training and certification are important for executing precautionary steps efficiently and regularly. By incorporating these avoidance strategies right into welding methods, the incident of porosity can be considerably reduced, leading to more powerful and much more reliable welded joints.
Value of Proper Shielding
Correct protecting in welding plays a critical function in preventing atmospheric contamination and making certain the stability of bonded joints. Shielding gases, such as argon, helium, or a blend of both, are commonly utilized to secure the weld pool from reacting with aspects airborne like oxygen and nitrogen. When these reactive aspects come right into call with the hot weld pool, they can create porosity, leading to weak welds with minimized mechanical residential or commercial properties.

Insufficient shielding can lead to different flaws like porosity, spatter, and oxidation, jeopardizing the architectural integrity of the welded joint. For that reason, adhering to proper shielding techniques is important to produce top quality welds with minimal defects and make certain the long life and dependability of the welded parts (What is Porosity).
Tracking and Control Methods
Just how can welders efficiently monitor and control the welding procedure to guarantee optimal outcomes and prevent flaws like porosity? see this page One key approach is through making use of sophisticated surveillance innovations. These can consist of real-time monitoring systems that give comments on criteria such as voltage, current, take a trip rate, and gas flow prices. By continually keeping an eye on these variables, welders can identify variances from the ideal conditions and make prompt adjustments to avoid porosity development.

Furthermore, executing correct training programs for welders is vital for keeping track of and regulating the welding procedure effectively. What is Porosity. Informing welders on the value of keeping regular criteria, such as correct gas securing and take additional reading a trip rate, can aid protect against porosity concerns. Normal evaluations and qualifications can likewise make sure that welders excel in surveillance and regulating welding procedures
Moreover, making use of automated welding systems can enhance monitoring and control capacities. These systems can precisely regulate welding criteria, minimizing the probability of human error and ensuring regular weld top quality. By integrating advanced surveillance modern technologies, training programs, and automated systems, welders can successfully keep track of and control the welding procedure to reduce porosity defects and attain top notch welds.
Final Thought

Report this page