What is Porosity in Welding: Finest Practices for Avoiding Porous Welds
What is Porosity in Welding: Finest Practices for Avoiding Porous Welds
Blog Article
Porosity in Welding: Identifying Common Issues and Implementing Ideal Practices for Prevention
Porosity in welding is a prevalent problem that usually goes undetected till it causes significant troubles with the integrity of welds. This usual defect can endanger the toughness and longevity of bonded structures, positioning safety dangers and leading to pricey rework. By comprehending the origin of porosity and executing efficient prevention strategies, welders can considerably boost the top quality and integrity of their welds. In this discussion, we will certainly discover the key aspects contributing to porosity development, examine its harmful effects on weld performance, and discuss the ideal techniques that can be adopted to reduce porosity event in welding processes.
Common Sources Of Porosity
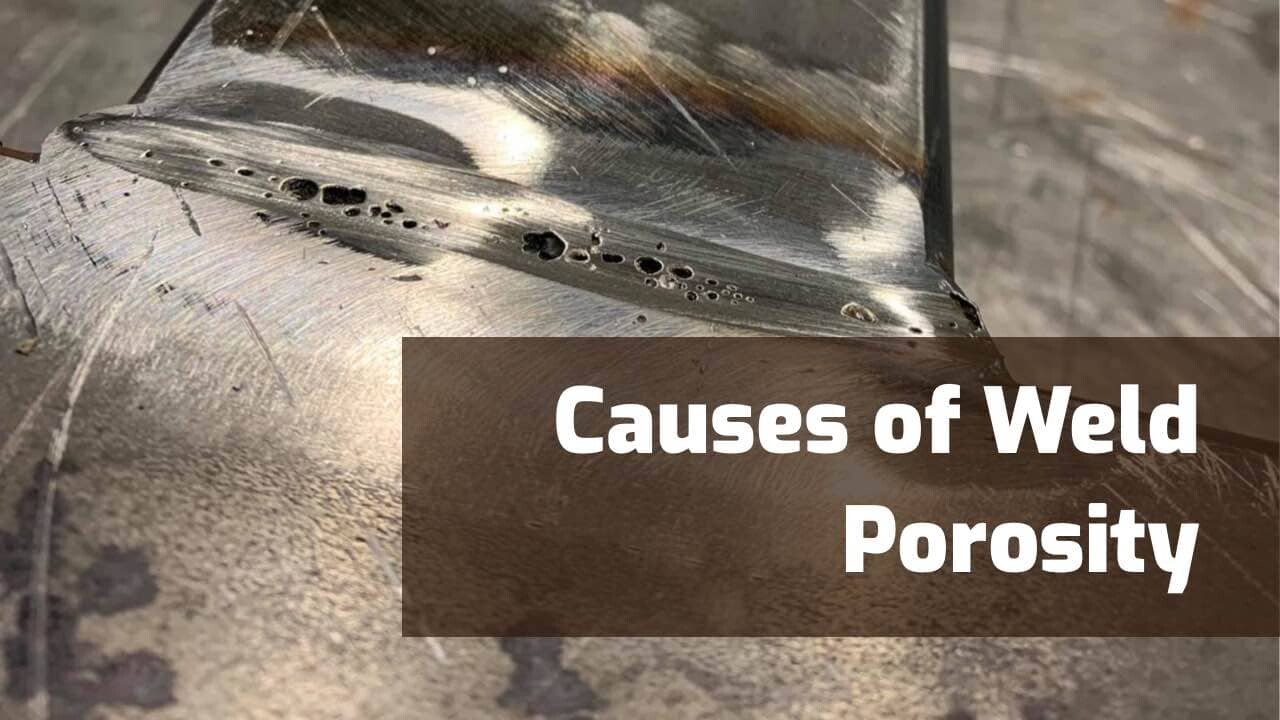
Another constant offender behind porosity is the visibility of impurities externally of the base metal, such as oil, oil, or rust. When these contaminants are not effectively eliminated prior to welding, they can vaporize and come to be entraped in the weld, triggering issues. Making use of unclean or wet filler materials can present pollutants right into the weld, adding to porosity problems. To alleviate these common root causes of porosity, complete cleaning of base metals, correct shielding gas selection, and adherence to optimal welding parameters are vital methods in achieving high-grade, porosity-free welds.
Influence of Porosity on Weld Quality

The presence of porosity in welding can considerably compromise the architectural honesty and mechanical homes of bonded joints. Porosity creates gaps within the weld steel, deteriorating its total stamina and load-bearing capability. These voids function as tension concentration points, making the weld much more at risk to splitting and failure under applied lots. Additionally, porosity can reduce the weld's resistance to rust and various other environmental aspects, even more lessening its longevity and performance.
Welds with high porosity levels have a tendency to display lower influence stamina and reduced capability to warp plastically before fracturing. Porosity can hamper the weld's capacity to efficiently transfer pressures, leading to premature weld failure and possible safety and security risks in crucial structures.
Finest Practices for Porosity Prevention
To improve the structural integrity and quality of bonded joints, what particular actions can be applied to lessen the incident of porosity throughout the welding procedure? Utilizing the appropriate welding method for the specific material being bonded, such as changing the welding angle and weapon position, can further avoid porosity. Normal examination of welds and immediate removal of any type of concerns identified during the welding procedure are important methods to protect against porosity and generate high-quality welds.
Relevance of Appropriate Welding Methods
Carrying out appropriate welding strategies is vital in ensuring the structural stability and quality of bonded joints, building on the structure of reliable porosity avoidance steps. Welding strategies directly influence the overall strength and toughness of the welded framework. One essential element of correct welding strategies is keeping the right warmth input. Excessive heat can result in boosted porosity because of the entrapment of gases in the weld pool. web link Conversely, insufficient heat may result in incomplete fusion, developing potential powerlessness in the joint. Furthermore, utilizing the appropriate welding specifications, such as voltage, current, and travel rate, is crucial for accomplishing sound welds with very little porosity.
Additionally, the selection of welding process, whether it be MIG, TIG, or stick welding, should straighten with the specific demands of the task to make certain ideal results. Correct cleaning and prep work of the base metal, as well as picking the appropriate filler product, are likewise crucial components of proficient welding methods. By adhering to these finest practices, welders can decrease the threat of porosity formation and create top notch, structurally audio welds.

Examining and Quality Assurance Actions
Quality control measures play an essential duty in verifying the stability and integrity of welded joints. Checking procedures are important to identify and avoid porosity in welding, ensuring the toughness and toughness of the last product. Non-destructive testing methods such as ultrasonic testing, radiographic screening, and aesthetic evaluation are typically employed to identify potential issues like porosity. These techniques enable the analysis of weld high quality without compromising the stability of the joint. What is Porosity.
Post-weld assessments, on the navigate to these guys other hand, assess the final weld for any type of issues, consisting of porosity, and validate that it meets defined standards. Executing an extensive top quality control plan that includes detailed testing procedures and examinations web is vital to minimizing porosity concerns and making certain the overall high quality of bonded joints.
Verdict
Finally, porosity in welding can be a common issue that impacts the top quality of welds. By identifying the usual root causes of porosity and applying best practices for prevention, such as proper welding strategies and testing actions, welders can make certain premium quality and trustworthy welds. It is important to focus on prevention approaches to lessen the event of porosity and maintain the honesty of bonded structures.
Report this page